Owensboro health regional hospital
Owensboro, Kentucky
Sharon Jankiewicz
Structural Option
![]() | ![]() | ![]() |
---|
Building Statistics
General Building Data
Primary Project Team
Building Name
Location
Occupant
Function
Size
Levels
Construction Dates
Cost
Delivery Method
Owensboro Health Regional Hospital
Owensboro, Kentucky
Owensboro Health
Hospital and Medical Campus
780,000 SF
Bed Tower and Spine: 9 Stories
Diagnostics and Testing Center: 3 Stories
April 2010 - June 2013
$385 Million
Integrated Project Delivery
Client
Owner Representative
Construction Manager
Architect
Structural Engineer
MEP/IT Engineer
Civil Engineer
Geotechnical Engineer
Ground Improvements Designer
Connection Design
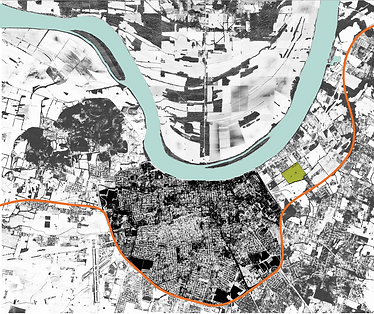
Owensboro, Kentucky
Route 60
Ohio River
Indiana
Map courtesy of HGA
Project Delivery
Design of this new hospital began during a tough economy. The project team mutually decided that construction cost would not exceed $385 million so $5 million was added to the scope of work without exceeding the budget. Operating on a "paper light" process, the project team was able to utilize BIM technology in order to communicate efficiently and effectively. Efforts were made to include prefabricated building systems and innovative scheduling processes.
Zoning
The building site was originally a soybean field and has been re-zoned for use as a hospital through the Owensboro Metropolitan Zoning Ordinance.
Historical Requirements
No historical requirements due to greenfield site.
Architecture
The most striking feature on the site is the nine story curved bed tower as part of the architectural theme "a river runs through", responding to the site's close proximity to the Ohio River. Landscape and architecture blend together to create an inviting place to relax and heal. The curved Bed Tower and Spine are anchored by the rectilinear Diagnostics and Testing Center. Courtyards, green spaces, and a roof garden are incorporated throughout the site for static relaxation, and paths weave to encourage physical activity. The Bed Tower and Connecting spine are both nine stories tall with an additional mechanical penthouse going up to the tenth story on the Bed Tower. The Diagnostics and Testing Center is three stories tall but it was designed for a vertical expansion of three additional levels, as well as horizontal expansion. Each section of the building is separated by seismic building joints.

Aerial View courtesy of HGA
Medical Office Building
Diagnostics and Testing Center
Spine
Central Utility Plant
/Support Services
Using a natural palette, the building's facade reflects the surrounding landscape, primarily consisting of stone, wood veneer, and glass. The glass curtain wall along the curved massing of the building creates a sequined dress, reminiscent of the nearby Ohio River highlighted by strong horizontality of the mullions. The stone is 4" quarried Fond du Lac laid in a coursed random ashlar pattern with limestone accents. The curtain wall system uses 3 1/4" mullions with 1" Viracon glass of various colors.

Curtain Wall Section

Interior Courtyard courtesy of HGA
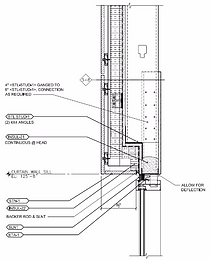
Stone Wall Section
Roofing
The roof of the Bed Tower and Spine is single-ply adhered roof and the Diagnostic and Testing center uses single ply ballasted, tapered on metal deck. The women's courtyard located on the third level is an intensely vegetated roof assembly with liquid applied roofing membrane and an irrigation system. Three built up earth berms are made out of geofill blocks and light-weight aggregate.


Sustainability
Although not LEED Certified, the project does meet stands should the owner wish to pursue official certification. Located on a what was previously a soybean field, the project team revitalized the site by restoring 70% to a naturalized state and has the honor of being the first Audubon International Certified Signature Sanctuary in the state of Kentucky and the first hospital to receive this distinction. A natural resource management plan was created to guide implementation of wildlife conservation and habitat enhancement, water quality monitoring and management, energy efficiency, and integrated pest management. The topography of the site is all interconnected for stormwater management and was created in order to raise the building above the 500 year flood plain level. Stormwater runoff from rooftop gardens and additional heavy rainfall are stored in the ponds to irrigate the site during dry periods. Other sustainability features include LED lighting, energy star rated computers and appliances, heat recovery chillers, recycled and locally sourced materials, and stormwater bioswales in the parking lot.
Structural System
Foundation
Before any changes were made to the site, it was originally classified as Site Class F with a bearing pressure of 4,000 psf. The entire building footprint has 16" grout columns installed in an 8 foot triangular grid at depths ranging 35 feet to 50 feet. As a result of this proprietary solution, the site is now considered Site Class D and the bearing pressure is 4,500 psf. The foundation primarily consists of spread footings with piers underneath most columns and mat foundations under the two braced frames in the Spine. Lateral steel column base plates are encased in concrete and set on reinforced concrete piers. The ground level of each portion of the building is a 5" concrete slab on grade with fiber reinforcement and a strength of 4,000 psi.
Gravity Framing
The entire project utilizes composite steel framing with 3" composite metal deck and 3½" lightweight concrete reinforced with 6x6W2.1x2.1 welded wire fabric. Due to the large variety of systems in each section of the building, the scope of this thesis will only include the Bed Tower and Spine. Bays in the Bed Tower and Spine follow a radial grid. The two bays across the width of the Bed Tower are approximately 32'-2" by 32'-7" and 28'-7" by 40'-7". Infill beams are either W16x31 or W21x44 with W24x55 girders. In the Spine, there is one bay of approximately 27'-10" with 9'-0" cantilevers on either side. Infill beams are various sizes, including W16x26, W18c35, and W21x44. Gravity columns are spliced every two stories ranging between W14x90 to W14x211
Lateral System
Special Moment Frames (SMF) are located in the radial and circular directions of the Bed Tower and in the radial direction of the Spine. In the circular direction of the spine, two Special Concentrically Braced Frames (SCBF) resist lateral loads. Beams in the Bed Tower are W36x150 in the radial direction and W24x68 girders in the circular direction. The Spine has five moment frames in the radial direction with W30x108 and W33x130 girders. Diagonal bracing within the SCBF consists of HSS 7x7x½ welded to gusset plates with W24x55 beams. Lateral columns are all W30's ranging between 162 lbs. to 391 lbs. per linear foot.
Mechanical System
Each level of the Bed Tower has two mechanical rooms at the North and South ends with Direct Outside Air System air handling units to supply all the patient rooms. Variable Air Velocity boxes regulate the CFM into each room. All air handling units are located on a 12" concrete pad. Three 600 BHP boilers are located in the Central Utility Plant and three 1,325 ton chillers provide hot and cold water for fan coil units.
Lighting
Lighting in the patient rooms consist of a recessed linear fluorescent 2'x4' troffer and the corridor has 4' linear fluorescents. Curtain wall is located on the south side of the building in order to maximize the amount of daylight that enters into patient rooms. Perimeter columns are located between adjacent rooms so they do not obstruct daylighting. 6" metal halide downlights are used to light the two story lobby space. Exterior metal halides are located in the courtyards to highlight the intricate landscaping. Emergency lighting is provided throughout the building connected to the backup power system.
Electrical System
Owensboro Health requires emergency power which is provided in the form of a rack-mounted uniterruptible power supply (UPS). The main electrical room for the building is located in the Central Utility Plant. Power is distributed from the main electrical to all other building sections with certain panelboards being classified as "critical". Feeders are separated between equipment loads such as HVAC equipment and normal distribution. Panelboards are 3 phase, 4 wire at 480/277 volts.
Construction Management
Integrated Project Delivery allowed all members of the project to be involved very early on and implement changes to design without dramatically increasing the project cost. Utilizing BIM technology, the project team operated on a "paperlight" process, ultimately saving $300,000. Instead of setting deadlines first, a pull schedule determined tasks to be achieved and then deadlines were set. Efforts were made to use prefabricated assemblies, such as structural steel components, plumbing, and HVAC assemblies. Work was sequenced from top down to minimize material transfer and traffic through finished spaces. Construction began April 2010 and was completed June 2013, with the project team coming in on budget at $385 million.
Telecommunications
Smith, Seckman Reid was the main technology contractor, handling the nurse call, security systems, and audio/video systems. By having one point of contact for all telecommunications, all of the cables were able to be pulled at the same time and prevent damage and the added time of multiple pulls. There is one telecomm room located on each level of the Bed Tower and Spine.
Circulation
The main lobby in the Spine has a bank of four elevators in the center and there is a staircase located at the north end. The Bed Tower has a bank of six elevators located at the intersection of the Bed Tower and Spine. Additional staircases are located at the two ends of the Bed Tower and another one is located adjacent to the elevator bank.
Fire Protection
The entire building is fully sprinklered, complying with NFPA 13, consisting of primarily a wet automatic sprinkler system. 6" standpipes are located in each stairwell with a 2½” fire department valve. Any fire protection piping that crosses the seismic building joints has a "Metraflex Co." Metra Loop Fitting to accommodate building movement. All partitions between patient rooms and the corridor are smoke tight rated and partitions around workrooms located in the middle of the corridor have a one hour fire rating.
Facade
Bed Tower